发光二极管一直以来都被当作低成本的指示灯用在各种电子产品上。目前,它们已经成为强大的光源,可用于室内照明、标识牌、显示屏和装饰照明应用。与白炽灯和荧光灯相比,由于产生相同亮度所消耗的能量要小得多,LED的地位正在日益攀升。能源是本世纪最为热门的话题之一,而且会很快成为世界各地设计人员需要考虑的最重要问题之一。
对灯具制造商而言,使用LED具有诸多优势。不过,试图尽早赶上LED浪潮的厂商数量也不少,因此产品的差异化非常重要。另外,当能耗和人力成本成为设计需要考虑的主要问题时,大型照明设备也几乎需要“智能化”。让灯具具备与“母”控制器通信、监测自身状况、根据监测结果调整工作模式、在失效后能够进入安全状态的能力等都是对新一代LED灯具的期望。本文将探讨部分适合于LED灯具的“智能化”选择及其实现步骤。
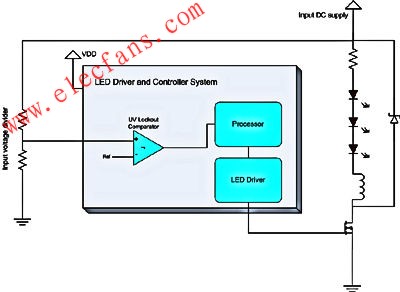
输入低电压闭锁:
LED驱动系统的输入电压一般是直流电压。电源由离线的AC-DC转换器或者总线提供。除了为LED驱动器供电,电源还用于为系统中的控制器供电(需先转换为适合控制器使用的5V或者3.3V电压)。控制器电源一般设计为当输入电压略高于要求的输出电压时,就开始工作。比如,5V的调节器会在输入电压达到6-7V时就开始工作。不过,这个电源的稳态可以是为由5-6个LED构成的LED串、每串电流为1A供电的24V电源。一旦控制器加电,控制器就会假定电源可用并开启LED驱动系统(假设其配置如此),随后LED驱动系统将试图进入正常工作状态。如果此时输入的电压只有10V,要求电源提供的电流将远远大于稳态下的电流,系统将由于这种瞬发的电流突增而崩溃。这种超额电流需求也会超出线缆、连接器和输入电源其他组件的额定承受能力,可能导致系统永久损坏。
为了避免发生这种情况,系统应具有“低压闭锁”功能。采用的硬件是电阻分压器,可以逐步把输入电压降低到控制器的输入可以承受的范围。输入在内部与比较器相连。控制器(固件)的动作应该设计为只有输入电压超过正常工作的阈值时,电源部分才会启用。另外,并非比较器一开启,电压系统就马上启动。固件应对比较器的输出进行轮询,检查这种状态是否一致(因为比较器是组合逻辑电路的组成部分),然后再启动电源系统。图2是实现该功能的硬件原理图(简图)。
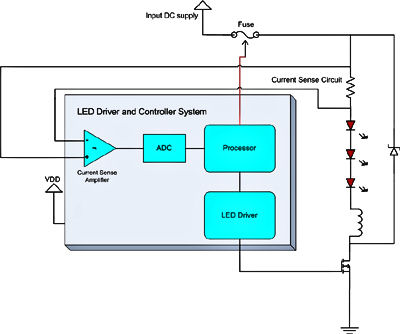
负载(LED)监测:
这里的负载具有经过LED且受调整的恒定电流。虽然电流调整系统已经在监测负载,这里的目的是确保有合适的负载电流流过。LED易于损坏,特别是在开路或者短路发生的时候。导致这些类型故障的原因包括线缆松动、连接器松动、PCB组装问题,等等。通道出现短路会导致MOSFET损坏(起开关作用)。鉴于这些系统的功率,在出现故障的情况下,会导致大电流的出现,并释放大量热量。为了保护系统及其周边免受故障的不良影响,控制器应具备实时监控负载状况的能力。
我们不妨考虑开路情况,其中供电流流经的路径不存在。如果让电流调整系统自行处理,它会让开关(MOSFET)一直开着,以试图让电流流往指定的地方。但这样不会解决问题。类似的,在出现电流不受控制地突增的短路情况下。反馈系统会试图关闭开关,但如果MOSFET已经损坏,它不会对这些控制信号做出响应,问题同样无法解决。
智能化的LED灯具应该能够检测这些状况,并将系统置于可以安全避免故障导致不良后果的状况。实现这种目标的其中一种方法是强制熔断保险丝,从而切断整个系统的电源。另一种方式是向“母”控制器发出某种信号,或者停止向“母”控制器发出某种信号,以指示故障状况。为此,系统必须能够首先监测负载电流或者电压值。为测量电流,在LED线路中引入了一个电流感应电阻,并将其两端的电压(在放大后)输入ADC。ADC的数字输出受处理器监控,并根据测得的电流值采取相应的行动。例如,如果通过LED的电流为500mA,但ADC只测得10mA,就可以视为出现故障。控制器随即向“母”控制器发出信号,启动“熔断保险丝”电路,强行熔断保险丝。
在诸如升压电路这样的电路中,存在着一个大容量电容器,故持续监控负载的电压非常重要。在升压系统正常工作的条件下,大容量电容器在开关断开的周期内充电,在开关闭合的周期内放电。如果负载出现开路,电容不会放电但充电仍在继续。如果置之不理,电容两端的电压会迅速升至很高,可能导致MOSFET这样的零件损坏。如果在连接松弛的情况下突然闭合电路,过充电的电容会在短时内造成过大电流通过负载,这样可能永久地损坏LED。
在大容量电容两端接上电阻分压网络,可以把输出电压降至微控制器可以处理的范围。信号随之输入到比较器,比较器的输出连接到可将其关闭的电流调节系统。当电压超过预设的限值,比较器就会打开开关,关闭系统。
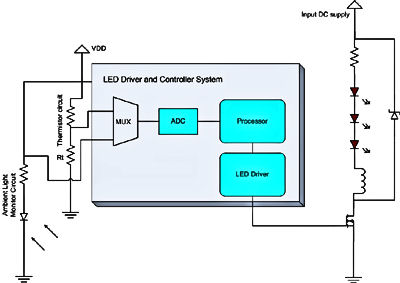
环境条件监测:
LED灯具会放置在各种环境中工作。在办公室环境中,如果灯具能够检测到人进出房间,在人离开房间后关闭或者降低亮度,对节能颇有好处。这可以节省电力,进而节省公司的电费。此外还可以有效利用LED,延长其使用寿命。
可以在系统内结合简单的环境光照传感器(光电二极管或者晶体管)来完成这项功能。这种传感器的输出一般是电流(大小取决于获得的光照强度),该电流可以用电阻转换为电压信号。电压信号随即通过其引脚提供给控制器,然后使用ADC转换为数字信号。控制器根据该值来确定合适的动作(降低亮度、关闭或者开启)。
LED自身也会发热,但与白炽灯所不同的是LED发出的热量随其终端传递,而白炽灯的热传递方向与光照方向一致。另外,LED灯一般安装在紧凑的空间内,散热条件恶劣。如果出现非正常的温度陡增,可能会引发各种后果,如零部件和LED的寿命下降乃至永久损坏,在极端的情况下甚至可能引发火灾。
总体而言,大致有两种监测系统温度的方法。其中成本较高的一种是采用基于I2C的温度感应器向控制器发送与温度相关的数字信号。当控制器具有内建的I2C接口时,如PowerPSoC LED驱动控制器系列,这种方法涉及的处理器开销很小,因为温度值被直接报告了。另一种成本较低的方法是使用热敏电阻和一个普通电阻构成分压网络。分压信号输入到控制器,后者使用ADC将其转换为数字值,并根据温度情况采取相应的动作。处理器需要执行额外的工作来把数字值转换为温度的对应值。接着可以把热敏电阻的电压直接输入到比较器(类似负载电压监测的跳接功能)。比较器可以根据预设的阈值开启或关闭LED驱动系统。
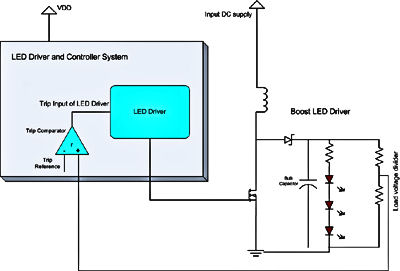
实时负载电流控制:
前文讨论了如何监测负载电流、电压和环境条件。智能灯具还应该具备根据监测到的状况改变其行为的能力。例如,智能灯具应该能够通过变更驱动电流或者输出的数字密度(PWM)来调整亮度。这可以根据环境条件、负载状况或者外部输入,如按钮或者通信接口来完成。动作可根据多种因素做出,并可对每种因素分配优先级。
例如,控制器应能对I2C或者UART这样的通信接口做出响应,并根据收到的数据调整亮度。不过,当输入电压降至闭锁阈值之下,或者温度升至安全值之上时,控制器可以逐步降低亮度(不考虑通信接口),并在设定值处关闭灯具。这样设定的动作可以有许多。
传统上,LED驱动器必须有由硬件(电阻值)设定的驱动电流,因此进行实时改变一般来说是不可能的。在软件可配置的LED驱动系统中,比如PowerPSoC,改变LED的驱动电流只需改写一些DAC寄存器。另外,采用软件可配置系统可以使用单一的硬件平台设计具有不同功能项的产品。
故障记录和诊断:
在灯具安装到大型建筑、停车场、街道等商业场合后,维修和更换会影响到成本和维护效率。如果控制器配有与“母”控制器通信的接口,用以规划维修和更换工作,该控制器也可用于记录和报告故障情况。
例如,灯具可能会因下列任何原因之一而损坏(或者保险丝主动熔断):
· 负载开路
· 负载短路
· 系统温度超过阈值的次数多于预设的次数
· 负载两端出现过压
· LED寿命终止或者出现过早老化
· 输入电压达不到闭锁值的时间超过预设时长。
这些状况都要求监测灯具的工作时长。这项功能只要求一个足够精确、能够记录工作时长的时钟(精确到秒)。控制器内部的大多数内部生成时钟都有一定的冗余度,可以决定计时系统的最终精度。更加精确的时钟一般都要求外部振荡器或者时钟源。
为了记录故障的原因,恰在系统关闭之前或者保险丝熔断之前的系统状况必须存储到非易失性介质中。带闪存的控制器可以把这些状况存储到闪存中。另一种方式是使用通过I2C接口与控制器相连的串行EEPROM器件。系统的工作情况和周边情况可以不断地、或者在保险丝主动熔断/系统关闭之前存储到EEPROM器件中。
在从设备中拆除故障灯具时,可以使用PC或者其他控制器读出非易失性存储器件,确定故障发生前的状况。读出的信息可用于确定零部件故障率、未知或者不可预测的环境状况,而且一般可以用来帮助工程师查找故障根源。
新型设计范例:
传统上,电源管理线路是完全用硬件实现的,唯一的配置性也是通过硬件提供的。其结果就是如果要创建产品的多种变形或者新产品,则需要独特的硬件组件组合。如果要缩短设计周期或者缩短产品投放市场的时间,就需要重新考察设计范例。例如,如果设计流程替代所包含的可配置软件模块,就可以大幅度缩短设计周期。其次,要让产品从竞争对手的产品中脱颖而出,或者脱离过去产品的窠臼,只需要变更软件配置并使用具有多重选择的同一硬件平台即可。软件可配置性还消除了采用硬件组件进行配置通常所面临的冗余度问题。如果整个产品系列能够基本同时投产或者依次投产,就能够增强进行差异化的竞争优势。